貼り(グルアー)について
--1024x768.jpg)
箱の製造の最終工程が製函と呼ばれている工程です。
貼り加工(グルアー)とは、箱の加工方法のことです。
次の流れで加工を行います。
箱の展開図の状態に板紙を打ち抜く 製函機のラインを通す 糊しろに糊を接着する 罫線で折りたたむ ベルトに通して糊を圧着させる
貼り加工(グルアー)オペレーターの発想1つで難易度の高い作業もでき、機械任せでなく、オペレーターのスキルの高低が受注できる仕事の範囲を大きく左右すると言っても過言ではありません。
当社では3台の異なるタイプの機械を設備し、箱の形や大きさ、材質などに応じて使い分け、多くの種類の箱をワンパスで糊貼り、製函できる体制を整えております。
この仕事の面白味は、3次元の理解が必要な事。プラモデルを作製するのに似た楽しさがあります。あなたのセンスで早く綺麗に仕上げて下さい。
それでは、実際の仕事の流れを見ていきましょう。
貼り(グルアー)加工作業前確認

貼り加工(グルアー)に入る前にまずやるべきことは『指示通りの加工を進めるための状態』を作ることです。
Aという商品の加工をしなければいけないのに、Bという商品を加工してしまってはどうしようもありません。
だからこそ、次にやるべき対象商品の確認する必要があります。
そして、加工対象商品の確認が取れれば、製造加工指示書を元にその対象商品の半製品であるブランク(打ち抜き加工で仕上がった箱の展開図の状態のもの)と原稿の確認を取ります。
作業指示書の確認
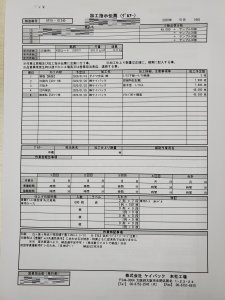
当社では朝一番にその日に作業する製造加工指示書を各貼り加工オペレーターに配布いたします。
状況の変化により加工機械を変更することもありますし、予定になかった商品を追加で加工をすることもありますが、原則として朝1番目の加工作業から最終の加工作業までを予定通りに順番に加工を進めて参ります。
各貼り加工オペレーターは配布された製造加工指示書を確認し、対象加工商品のブランクがラインにあるかどうかを確認します。
原稿とブランクの照合

製造加工指示書を元にまず確認しなければならないことが『原稿』です。原稿とは受注した商品を製造するために加工を進めていく上で正確に加工するための見本となるものです。原稿は商品の加工がスタートする1番目の加工から半製品状態の加工物と共に付いてまわります。
製造加工指示書と原稿を元にブランク(加工前の半製品状態のもの)が間違っていないかを確認します。
外装ケース(商品を収納するための段ボールケース)の確認
貼り工程は原則最終工程となりますから、加工が終わった段階で外装ケースに収納することになります。
いざ、本稼働に入ってから「外装ケースがない!」ということになると、収納する場所がなくなりますので、作業に入る前の確認事項の1つとしてチェックしておくべきポイントの1つとなります。
実際の確認作業は貼り工程のデリバリースタッフにお任せしますので、機械オペレーターは確認の指示を出すということになります。
貼り(グルアー)加工準備
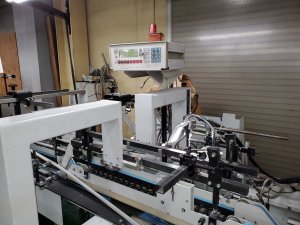
ブランクが間違っていないことが確認できると機械を本稼働させるための準備を進めていきます。
ブランクのセット
-300x225.jpg)
ブランクを貼り加工機にセットします。
ブランクのセットは機械の給紙部にセットするだけ、と言うと一見簡単な作業に感じられますが、この部分のセット状態で加工作業の良し悪し(加工しやすい、しづらい)が左右されると言っても過言ではありません。
機械調整
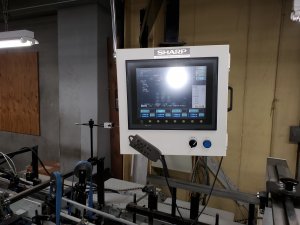
ブランクがセットできれば機械を本稼働させるための調整をしていきます。
ブランクを1枚ずつ機械に通し、ベルトに挟まれ、乗せられながらデリバリ部へと進んでいくわけですが、その間で、糊代に糊を接着させ、折り罫部を折り曲げ、最終的に折りたたんだ状態にして、ベルト圧着部へと流し込んでいきます。ここの調整作業が貼り加工オペレーターのメイン作業になります。
主に何の調整をするかと言うと大きく分けて2つ。『糊の接着の調整』と『折りたたむ状態の調整』です。
糊の接着の調整のポイントは3つ。
1つ目は糊の種類を間違えないこと。貼り加工(グルアー)で使用する糊には複数の種類があり、ブランクの素材や表面加工の方法などにより糊の種類を適性の良いものに変更します。
もちろん、生産性を考慮してできる限り糊の交換をせずに済むように加工の順番を決めますが、時と場合によっては1日の途中で糊を交換する必要性が出てくることもありますので、糊の選定には十分に気を付けなければなりません。
2つ目は糊を塗布する位置です。
糊を塗布する位置がずれてしまいますと、製函後に糊がはみ出てしまって外部付着(箱と箱がはみ出した糊によって引っ付いてしまう現象のことなど)や内部付着(折りたたんで製函した箱の内部がはみ出した糊によって引っ付いてしまい箱が開かない現象のことなど)を引き起こしてしまいます。
また、きっちりと糊代の端っこまで接着されていないことで、蓋が閉まらなかったり、強度が弱くなったりというような不具合が起こる原因にもなりますので必要な箇所に正しく糊を塗布するという事が重要なのです。
最後の3つ目は糊の塗布量です。
接着する糊の塗布量が多すぎますと、糊の接着位置のズレの時と同様、製函後に糊がはみ出てしまって外部付着(箱と箱がはみ出した糊によって引っ付いてしまう現象のことなど)や内部付着(折りたたんで製函した箱の内部がはみ出した糊によって引っ付いてしまい箱が開かない現象のことなど)を引き起こしてしまいます。
逆に接着する糊の塗布量が少なすぎますと、当然のことながら糊代部分の貼り合わせが完全に出来ずに製函が出来ていない状態の箱が出来てしまいます。場合によっては疑似接着状態となり(疑似接着とは一見接着しているように見えるが実は完全には接着できていない状態のこと)納品後にお客様の方で箱に商品をセットされる段階で疑似接着状態の部分が剥がれてくるという現象が起こったりすることもあります。
これらの不具合品を出さないためにも糊の接着状態の確認は重要な調整となります。
折りたたむ状態の調整のポイントはたった1つ。
折り罫の入ったところできっちりと折れているかどうかだけです。折り罫の入っている通りに折りたたみさえすれば、完全な箱に仕上がりますし、折り罫からずれて折りたたむことで歪な箱ができてしまう原因にもなります。
あえて付け加えておくと、折り罫通りに折りたたんだにも拘わらず、箱に仕上げた際に歪な箱が出来上がってしまったのであれば、その原因は打ち抜き加工(トムソン)時において折り罫を入れる位置がずれていたか、もしくは箱の設計そのものが間違っていたということが考えられます。
これらの不具合品を出さないためにも折りたたむ状態の確認は重要な調整となります。
この調整は、ブランクを1枚1枚ゆっくりと通しながら、各セクション(先の調整ポイント)でタイミング、位置等の微妙な調整をしてまいります。
本稼働前チェック

調整が終われば機械を本稼働させる前に、製品の加工状態の最終確認をします。
良品として万全な状態にかこうできているかどうかをここで隅々まで目を光らせます。
ここでのチェックが甘くなりますと、不具合品が発生する状態で加工を進めることになりますし、場合によってはそれが不良品としてクレームの原因となってしまいます。
貼り(グルアー)加工の本稼働
準備が終わればいよいよ本稼働です。
ここでのオペレーターの役割としては、準備段階でOKとした状態が最後まで保っているかどうかを逐一確認することです。
抜き取りチェック
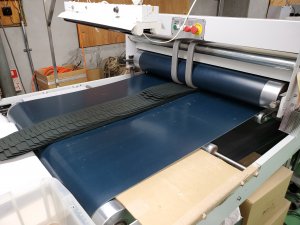
本稼働に入れば、安定稼働になるまではこまめに抜き取りチェックを行い、安定稼働に入ってからも定期的に抜き取りチェックを行うことで貼り加工が終わる最後まで不具合品が出ないようにします。
本稼働中の抜き取りチェックはデリバリスタッフの仕事になりますが、頻度を抑えるとは言え、加工責任者である機械オペレーターの定期的な抜き取りチェックは欠かせません。貼り上がり状態の確認をすることで、現状の機械の傾向を感じ取ることが出来、機械稼働中に微妙な調整を加えることで不具合品が出てしまう前に未然に防ぐこともできるからです。
最終製品チェック

本稼働が終われば最後のチェックです。間違いなく最後まで不具合品を出すことなく良品状態を保って加工が出来たかを確認します。
提出資料等の最終確認

加工が終われば各機械に設置されているタブレットにて加工データを入力し、製造加工指示書の記入、加工中にチェックを入れているチェックシートの記入をしてクリアホルダに収納し、次の加工作業へ進めるように整理します。
ここまでが貼り加工(グルアー)の仕事の流れとなります。
いかがでしょうか?ご興味を持って頂けましたでしょうか。
就職・転職希望の方は求人採用専用ページの方へどうぞ。
正社員の方はもちろん、アルバイト・パートの採用も都度行っております。諸条件等の詳細は求人掲載ページをご確認ください。
現職社員の声を聞きたい方は社員インタビューへどうぞ。