
「パッケージ作成~押さえておきたいテクニック~」というタイトルですが、この「テクニック」という部分を言い換えるならば「パッケージ作成~欠かさずやっておくべき事~」とでもいった内容と言えるかもしれません。
アナタが作るパッケージをより良いものとするべく細かく小さなコツのような内容を少しでもお伝えできればと思っておりますので、是非とも参考にしていただければ幸いです。
ということで、
今回は、パッケージの実製造に入る前におこなっておくべきテスト、おこなっておいた方が失敗を防げるテストについて幾つかずつ回を分けて書かせていただきたいと思います。
まずは・・・・・
何故テストが必要なのか
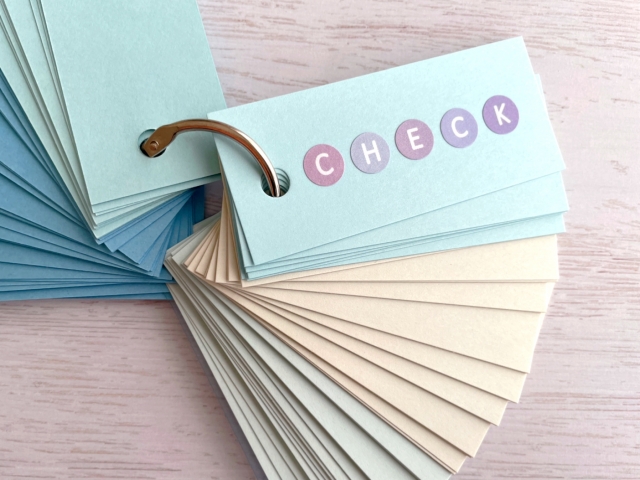
ということですが・・・
当たり前ではありますが製造前にテスト作業を差し込むということは、スケジュールやコストにも影響が出る可能性は高くなります。それでもテストしておくことで、より良いパッケージを作成する、且つ失敗の可能性を減らしておくことは大事なのではないでしょうか。
仮にテストをしなかったことで失敗した場合を考えてみましょう。その度合いにもよりますが、そのままでは使用に耐えない品となってしまったとしたらどうでしょうか。原因となる点を改めた上で作り直すとしても費用と時間は必ず掛かります。その責任はどこにかかるかはまた別としても、です。
またテストしておくことでより良いパッケージが出来上がった場合は、よりたくさん売れる・より良い反応が得られる可能性は上がると考えられますね。
たとえスケジュール・コストに影響が出ても予めそれを飲み込み様々なテストをしておくことは、メリット・デメリットもしくはリスク管理の観点からも決して損なことではないのではないでしょうか。他の作業と並行して行う事で最低限の日数で済む、比較的費用の掛からないテストだけでもしておく意味は大きく、必要なことなのです。
もちろん既に予算や納期が決まっていて動かせないなどよくある話であり、あくまで可能な限り、としか言えませんが。。。
ホワイトダミーの作成
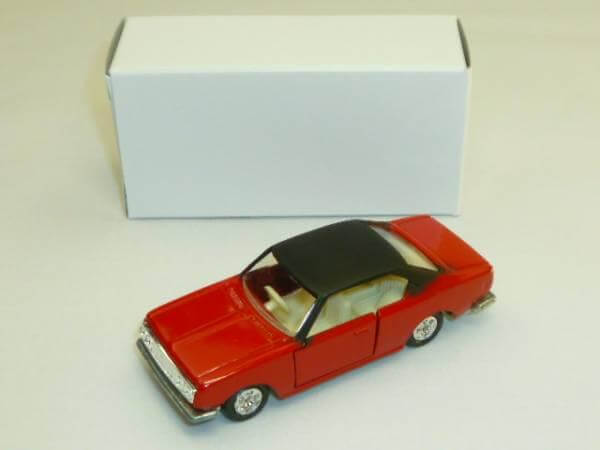
ダミーとは、形状・サイズを確認するために実際の製品と同じ形状や大きさの品を型作成前にCADカットなどで試作したものです。印刷なしの無地で作成したものがホワイトダミーと呼ばれており、近頃では色校正をカットして確認する校正ダミーなども増えてきましたが、まだまだ一番多い確認用ダミーです。サイズが間違っていないか、展開図では判り難いが組み立てた際に生じる問題はないかなどをテストするわけです。
アナタがパッケージの作成経験がある場合など、「えっ、コレって当たり前のことなのでは?」と思われるかもしれません。確かに、そのくらい基本的なテストであります。当社でも新規で抜き型作成する際には、基本的にダミーを作成してお客様に確認していただいてからでないと抜き型作成には入りません。
しかしながらその基本的なテストであっても、主に納期が迫っているなど理由によりお客様からの指示により行われない事もあるわけです。
もちろん、テストしない=失敗する、というわけではありません。わけではありませんが、過去には実際に、ダミー作成しなかったことが原因で、またホワイトダミーを作成するも実際に中身を入れてみてテストしなかった事が原因で製造後にサイズが合わないという事態が起きたことがあります。
特にサイズについては、中に入れる製品のサイズを計り間違えた、途中で変更になったのをうっかりしていたなど、ダミー確認したことで気付き修正したことで防げた事故は多々あります。当社側においても、よくよくチェックしてはおりますが抜き型データ作成時の計測ミスや入力ミスは起き得ることですので、ホワイトダミーの作成・確認には非常に重要なテストであり、今読んでいただいているアナタには是非とも「必須テスト」と捉えていただけたらと思います。
印字テストをする
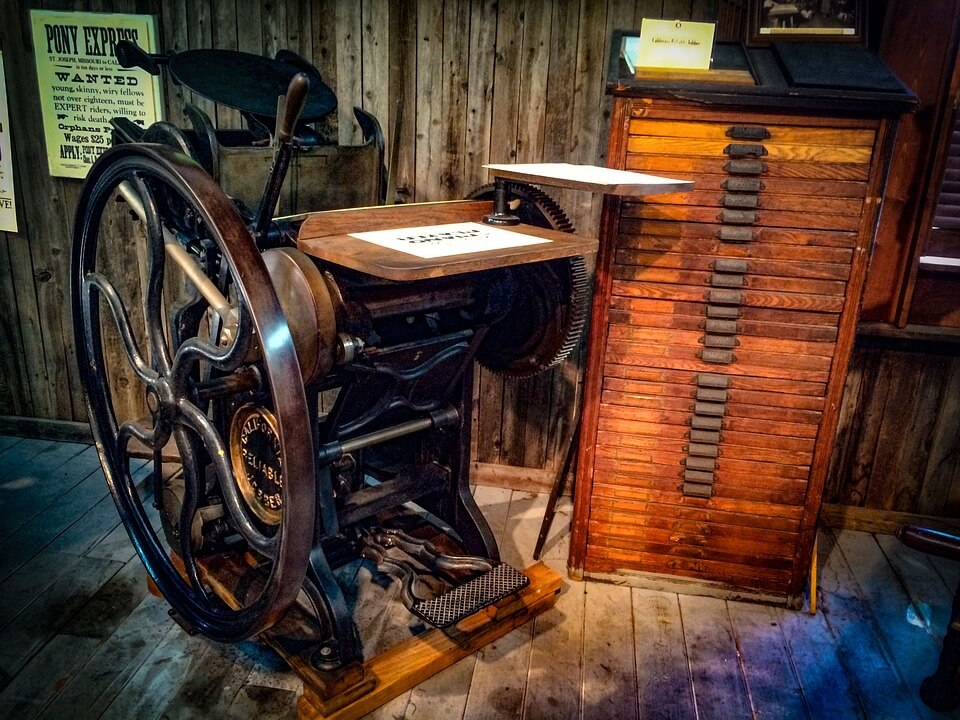
これも基本的なテストと言えるでしょう。それだけに重要なことと捉えてほしいテストではあります。
印字テストとは、パッケージ製造後にパッケージを組み立てて中の製品を入れるセットアップ作業の際などに『製造年月日』や『賞味期限』、『製造番号』などを印字する事が可能かどうかのテストです。先に挙げた印字は通常は当社から納品した先(セットアップ現場など)においておこなわれますが、使用する印字機の仕様によっては印字できない場合があります。主な理由としてはパッケージの表面加工との相性となります。ニス・ビニール・プレスコート・PP貼り・PET貼りなどパッケージの表面加工も色々あり、印字機にも種類があるため、新しくパッケージを作る際に今まで実績のない表面加工への印字となる場合には必ずテストしておいた方が良いでしょう。
例えばニスであれば、ニスの上へは印字できないことも多いのですが印字スペース部分のみニスを引かないようにするのは比較的簡単に出来ます。これがプレスコートになりますと、印字出来ることが多いようですが、印字出来ないときに印字スペースにはプレスコートをしないようにするためにはニスと比較して大きなコストが発生します。別の表面加工を検討する必要も出てくることでしょう。
いずれにせよ製造前に判っていなければ対処のしようがありませんね。後になって「印字出来ませんでした」というわけにはゆかぬ内容でもあります。印字される現場にもパッケージの製造前に確認し、少しでも不安がある場合には必ずテストしておきましょう。
余裕ある日程で
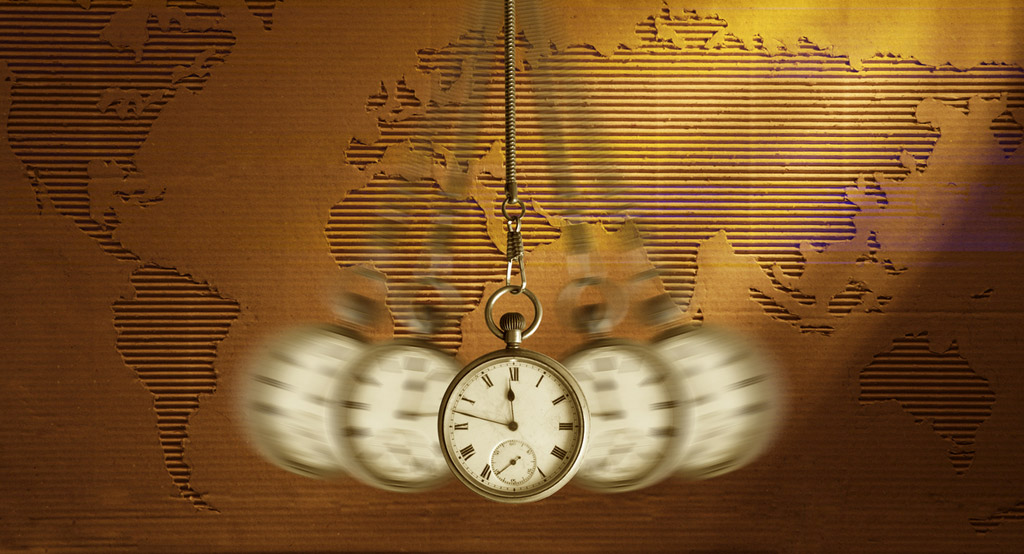
さて今回は2点、「ダミー」と「印字」について書かせていただきました。
回を分けて今後また別のテストについても上げていきますが、ここまでで既にお気付きの方も多いのではないでしょうか、まず以て時間・日程を確保することが大事であるという事に。最初に防いでおきたいのは、テストしておきたくても出来ない、そんな状況に陥らないようにするということです。製造自体はどれほど急いでも限界があり、急げばまた事故の起きる確率が高くなるわけで本末転倒となってしまいます。
決して簡単なことではありませんが、まずはご一考いただければと思います。